Our Process
Quality from Orchard to Export
At Goede Hoop Citrus only the finest fruit will do. That is why every piece of fruit we export is picked and inspected by hand.
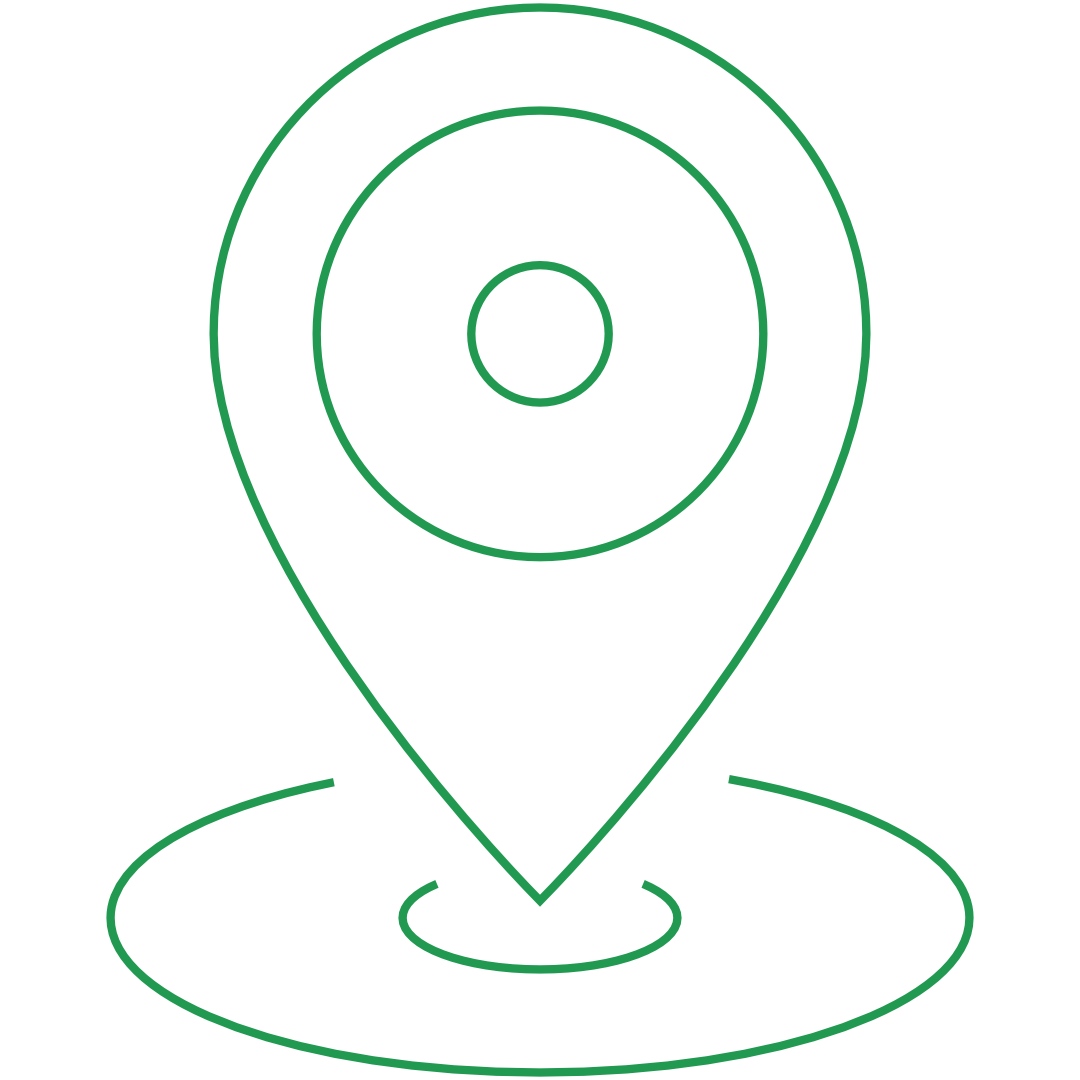
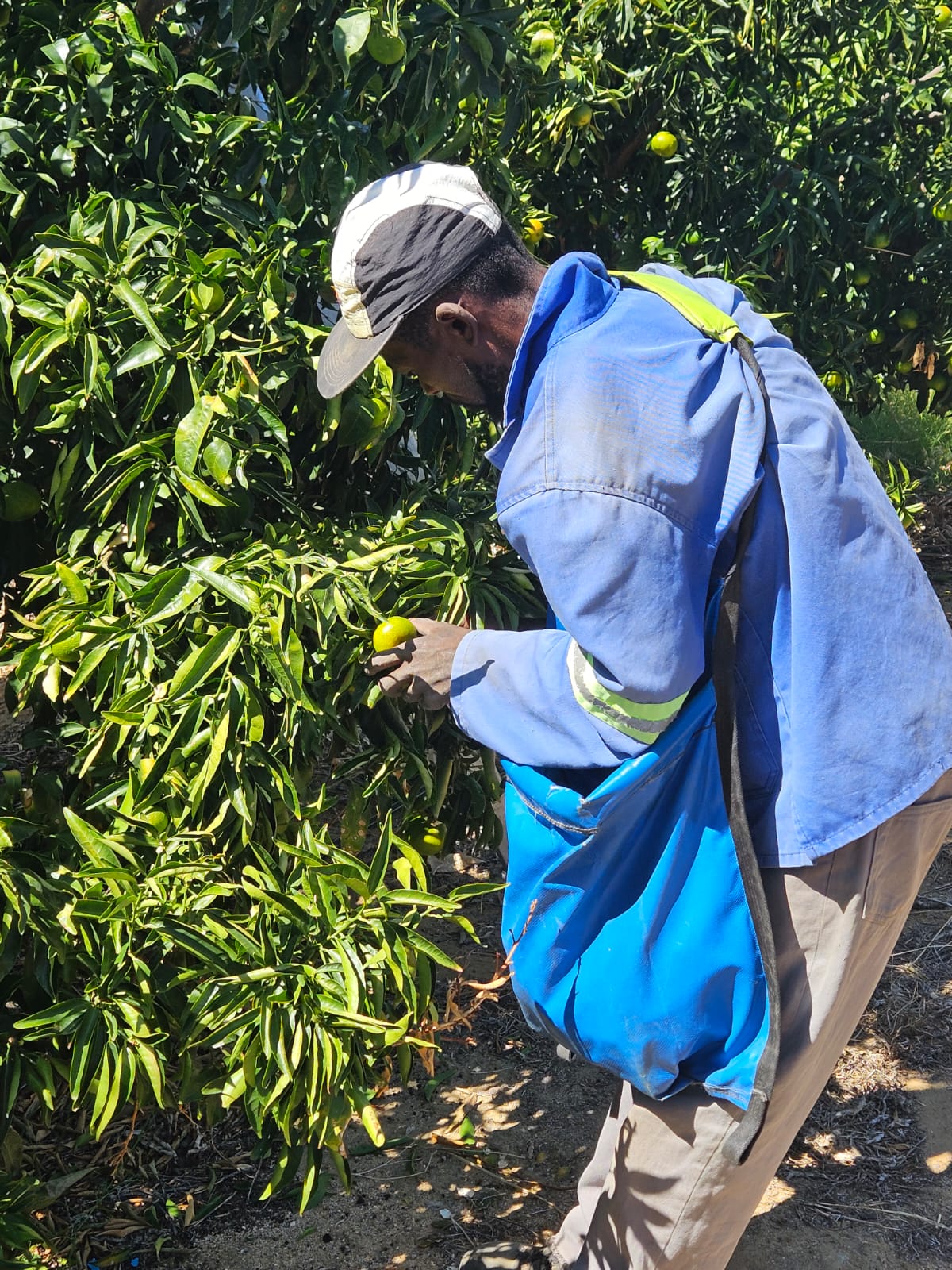
The Olifants River Valley, Piketberg, Porterville, and the Nuy Valley near Worcester are known for their agricultural activities, particularly Citrus fruit farming. After the fruit is harvested, it’s transported in crates to packing facilities where it is sorted, packed, and prepared for export.
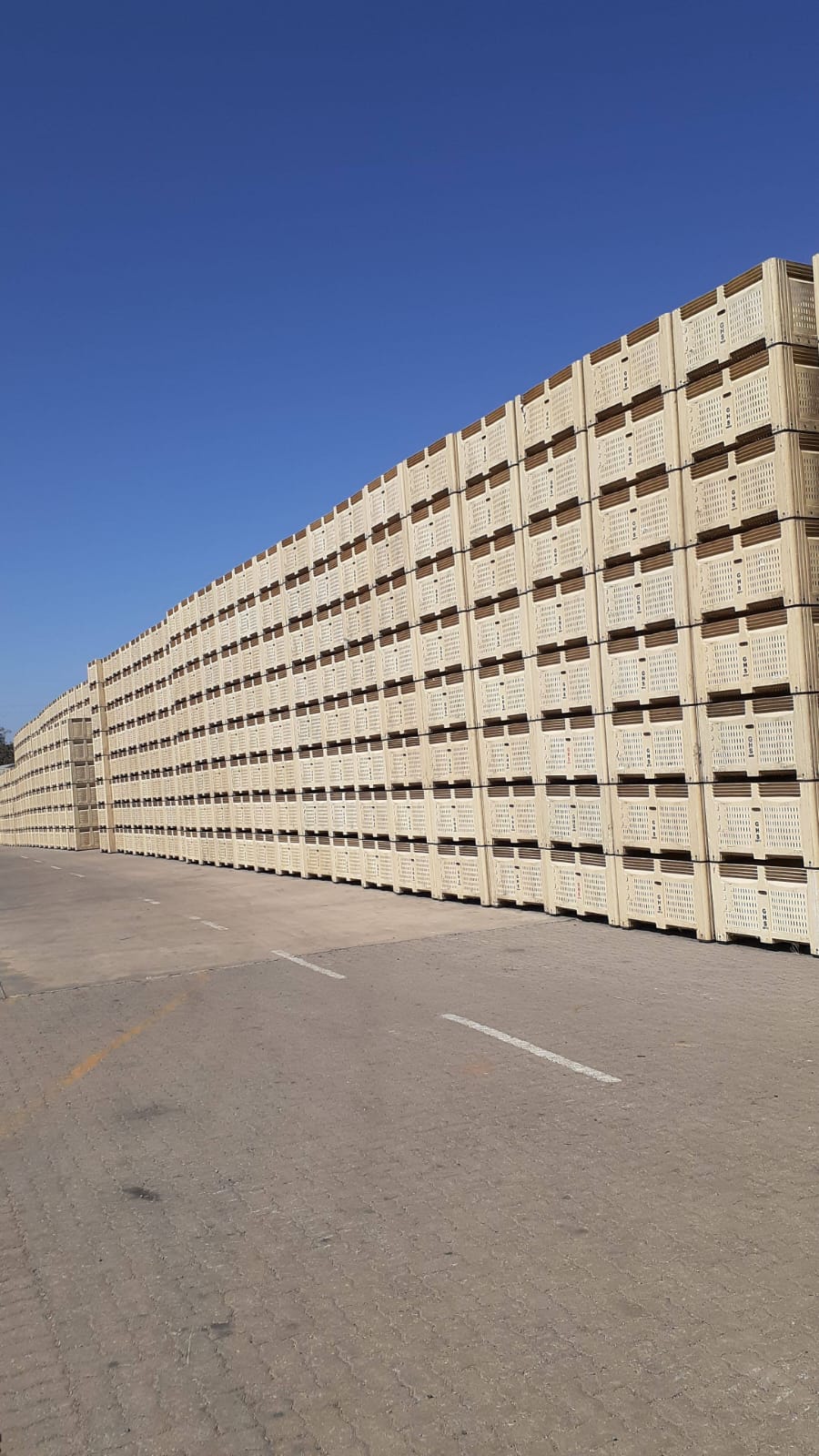
Once the crates are delivered to the Intake Inspection Centre, random fruit samples are taken for analysis. This process ensures that the fruit meets specific quality standards before it is processed further or packed for export. The analysis include the verification of the fruit for size, color, sugar content, and any signs of disease or damage. This step is crucial to maintaining the overall quality and safety of the produce

If the fruit does not meet the desired color standards during the intake inspection, it is allocated to the de-greening chambers. In the de-greening chambers, temperature, humidity, and ethylene gas levels are carefully controlled to ensure that the fruit reaches the optimal color for market standards without affecting its taste or quality.
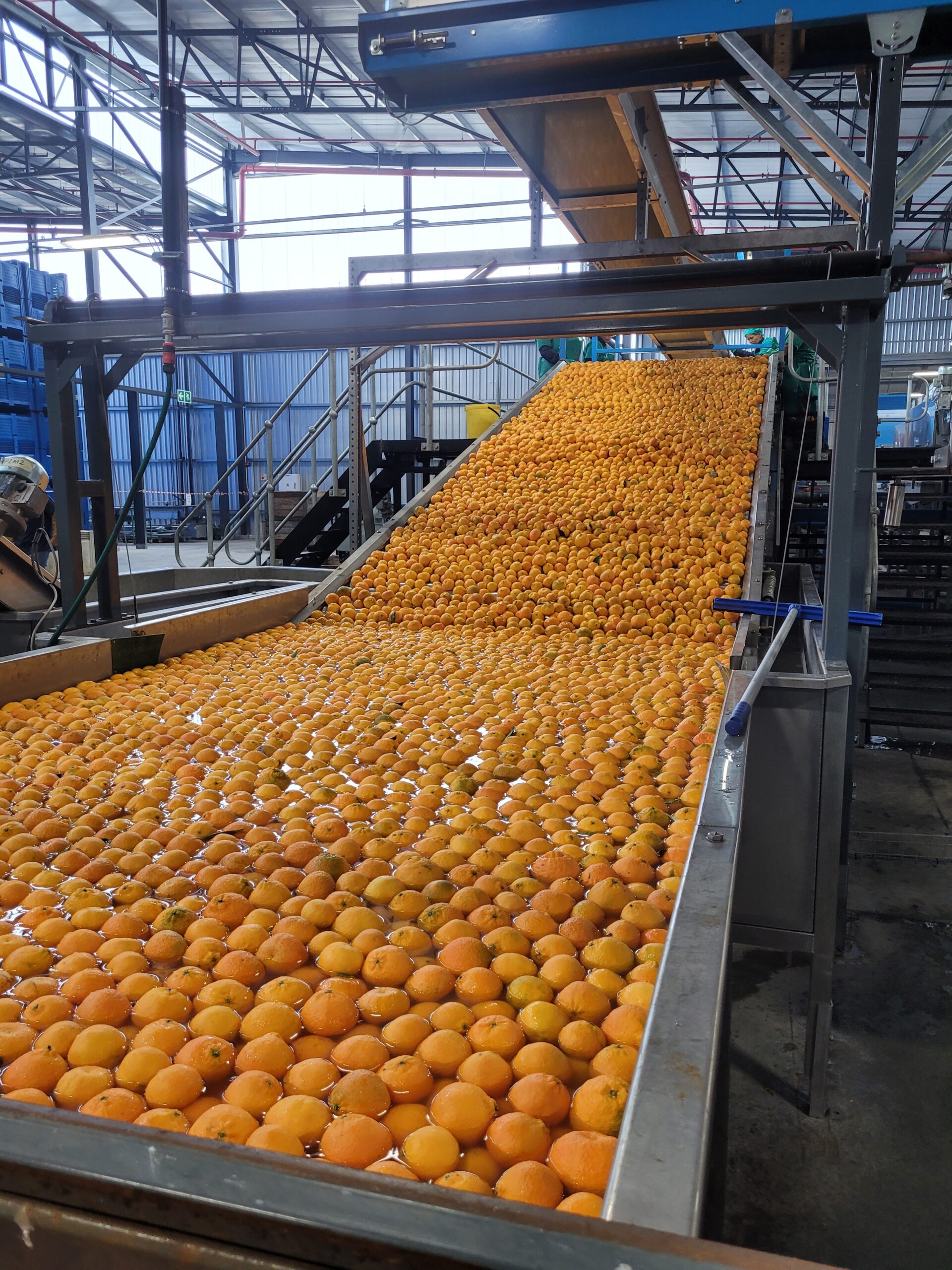
Before the fruit enters the packing plant, it undergoes a washing and treatment process. This step is essential for ensuring that the fruit is clean and free from dust or debris that might have been picked up during harvesting or transporting.
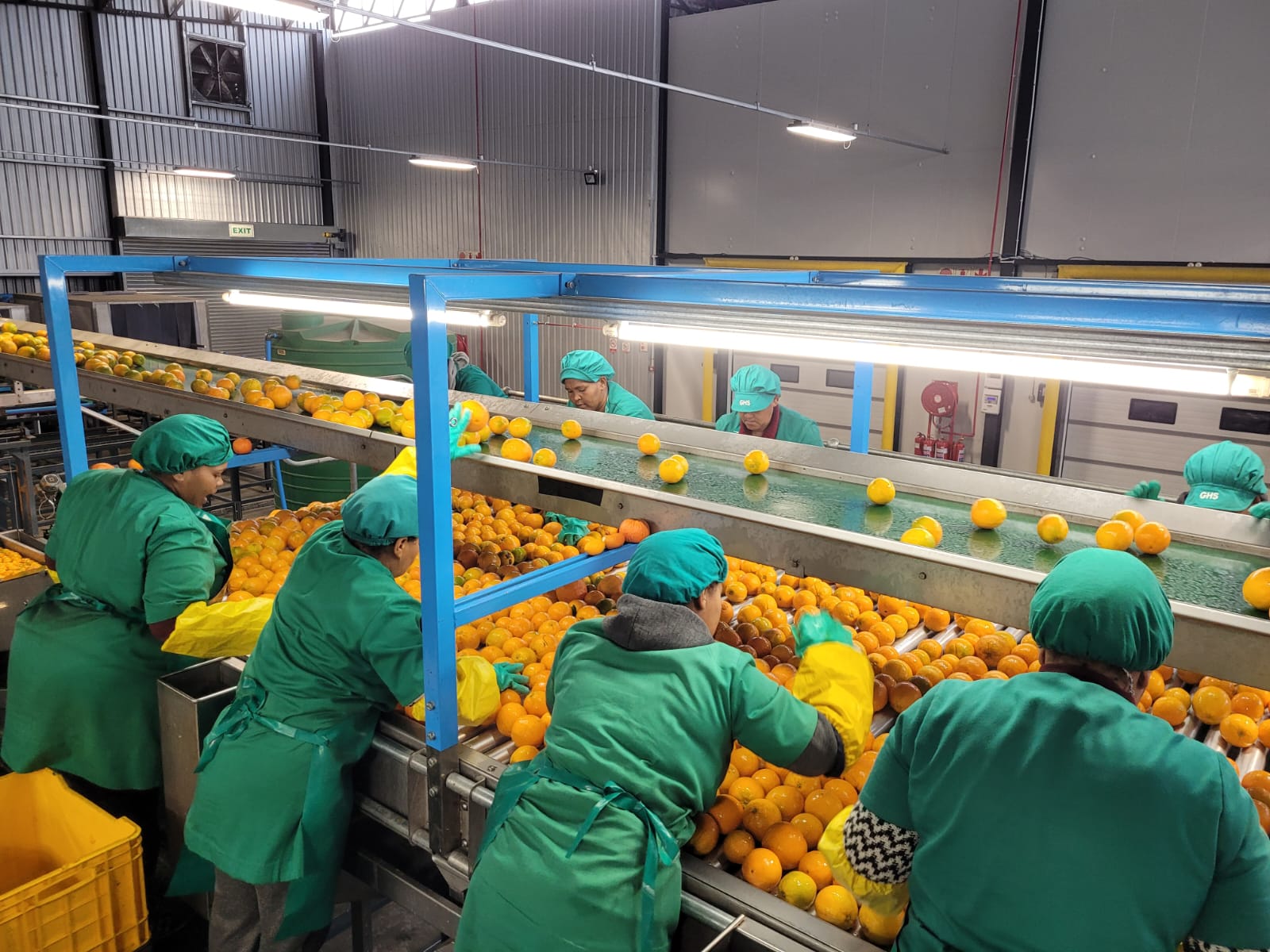
After the fruit is washed, treated, and dried, it moves on to the quality control stage within the packing plant. During this process, workers manually inspect and sort the fruit to ensure that only the highest quality produce is selected for export.

After passing through the quality control stage, the selected export-quality fruit receives a protective wax coating. This wax application serves two primary purposes: Enhancing the Appearance and Prolonging the Shelf Life of the fruit. The wax used in this process is food-grade and safe for consumption.
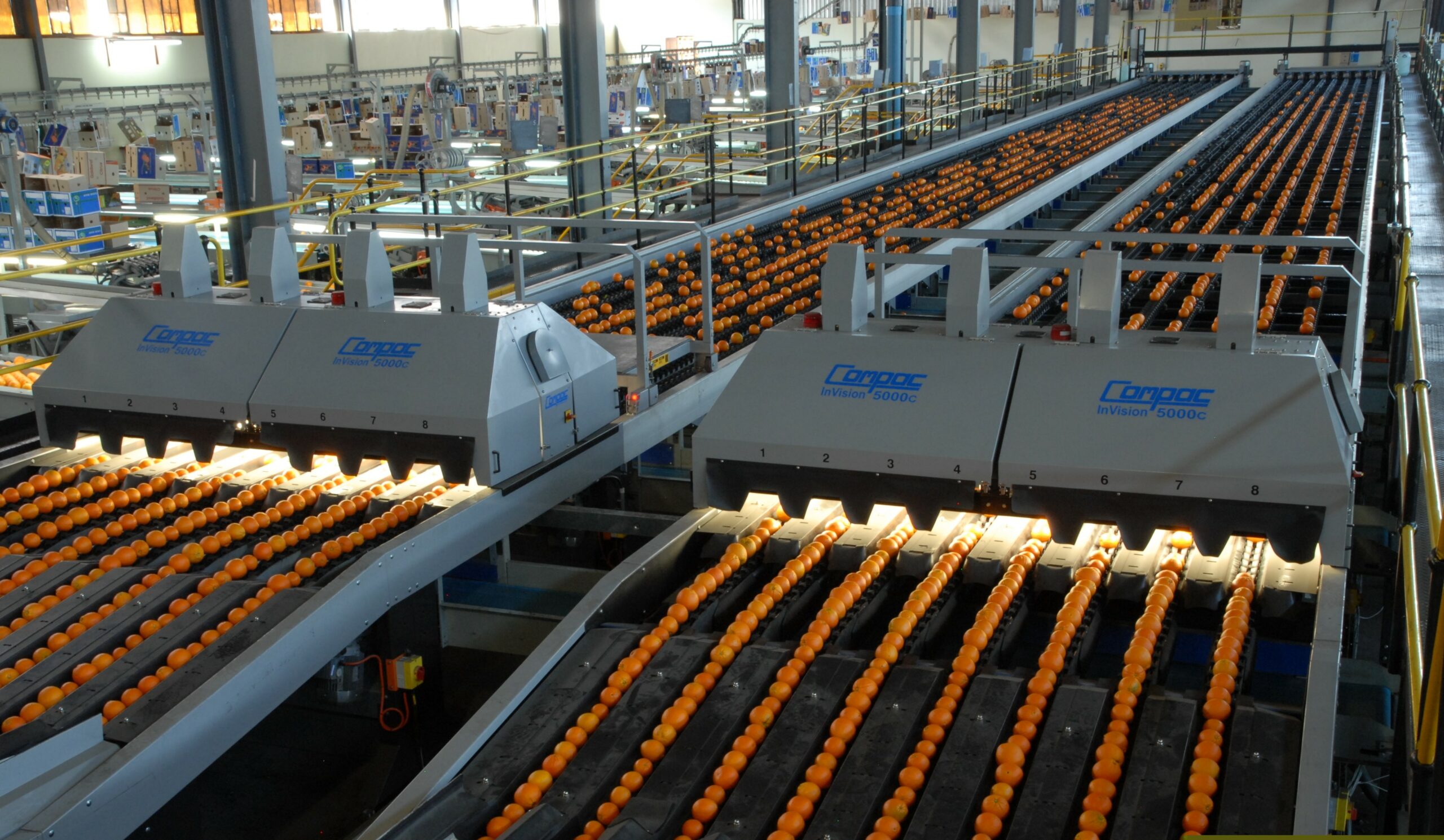
Once the fruit has been cleaned, treated, inspected, and received its protective wax coating, it moves on to a automated sorting process that sorts it by size and color. This sorting process is essential for categorizing the fruit into different grades, which helps determine how it will be packaged and where it will be distributed. This automated sorting process ensures consistency and efficiency, allowing large volumes of fruit to be sorted quickly and accurately.
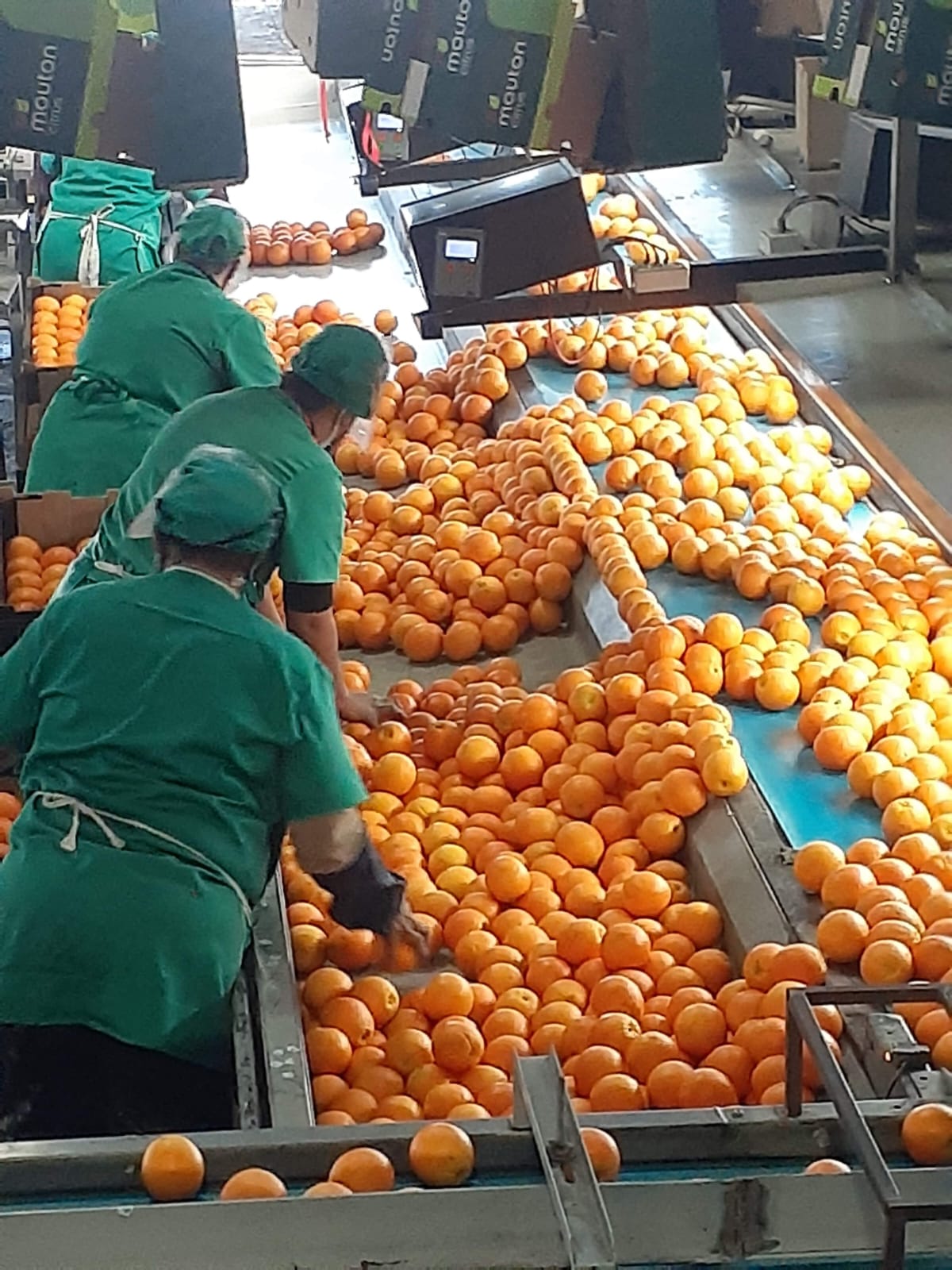
After the fruit is sorted by size and color, it reaches the final stage of the packing process, where skilled workers pack the fruit into individual cartons by hand. Despite the automation in earlier stages, this step is crucial for ensuring that the fruit is carefully handled and presented in a way that meets market and customer expectations. The packed cartons are stacked onto pallets, ready for inspection, storage or transportation.
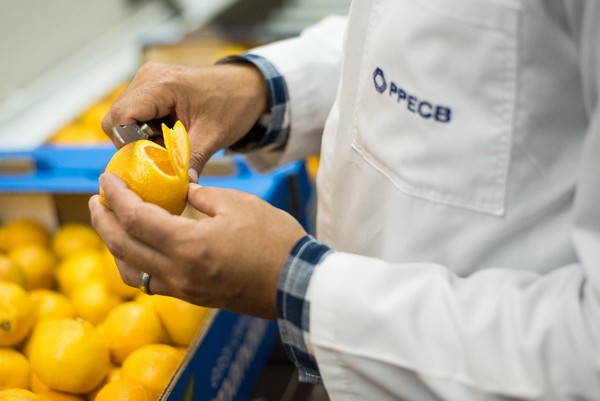
After the fruit is carefully packed into cartons, the next step involves an inspection by staff from the Perishable Products Export Control Board (PPECB). This inspection is crucial for ensuring that the packed fruit meets the strict quality and safety standards required for export.
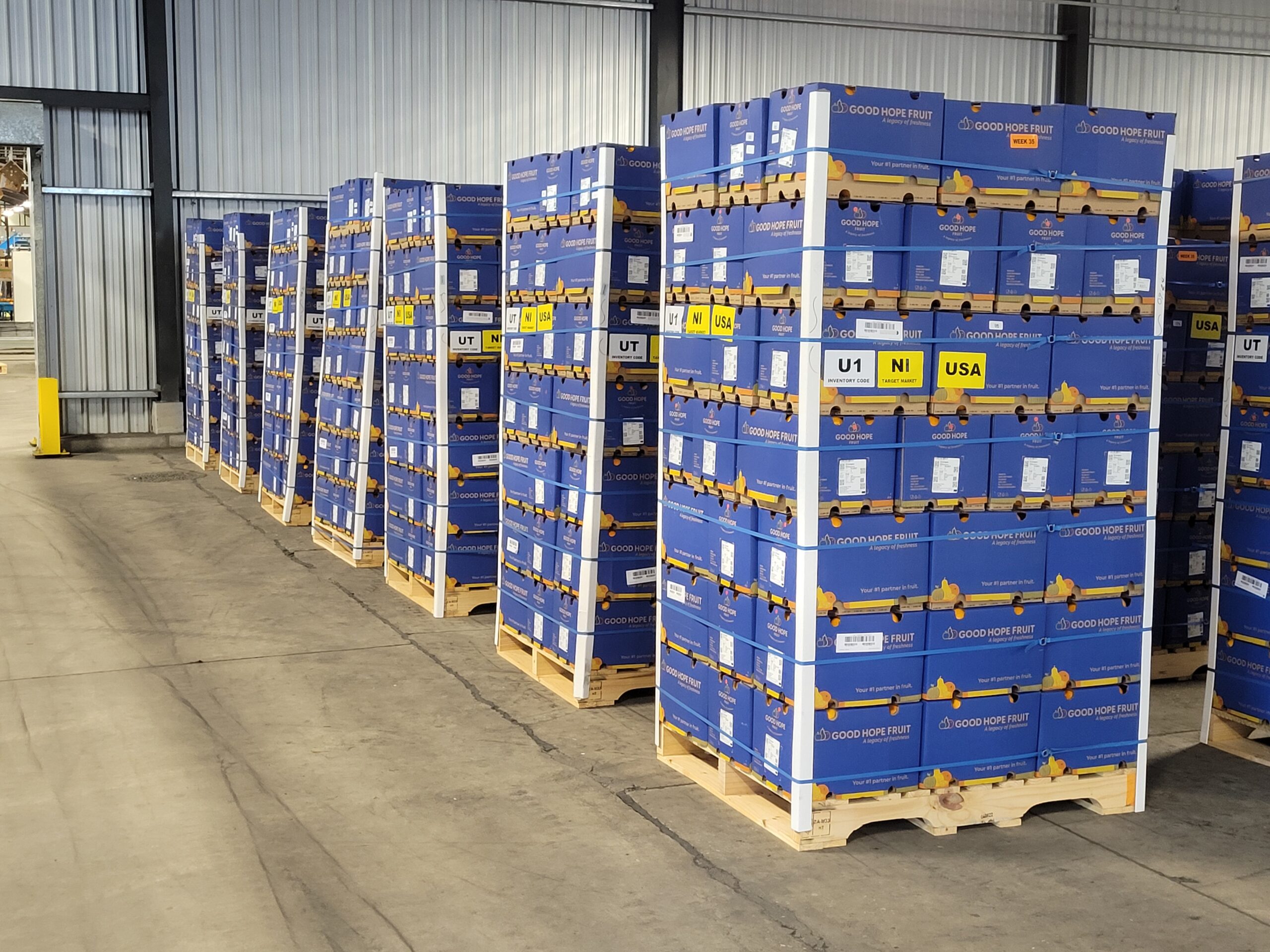
After the packed cartons of fruit pass the PPECB inspection and receive certification, they are ready for export.
Contact Us
Let's get in touch
Our team is waiting to hear from you.